The Moonfish design uses the inverted deck accurately marked out as the building jig for the frame. Here you can see that, after I marked out the positions of the bulkheads and stringers on the deck in pencil, I covered them with parcel tape and then remarked with permanent marker:
The tape is to prevent the frame sticking to the deck at this stage of assembly; the green polythene sheet serves the same function for the daggerboard/mast trunking assembly. The cleats around the sheerlines are screwed on temporarily and will be used when fixing the hull side panels to the frame.
I start the daggerboard trunk in two halves. When it was accurately dry assembled, I drilled it for dowels which will provide accurate and positive location during assembly:
I've learned the hard way that epoxy coated components are slippery and tricky to clamp together accurately !
Once those packing pieces were glued on, I then coated the trunk sides with glass cloth and epoxy:
These will need a second coat of epoxy before assembly of the trunk. Once assembled, the ends formed by the packing pieces will be covered by glass tape and epoxy.
Next up is the bow stringer, which gets doublers at the bow and packing pieces where it goes into the daggerboard/mast trunking:
This will be the last post on construction until 2014, as we are decamping to Pembrokeshire for the Christmas and New Year. I listened to my last student presentations today, although I do have the coursework for their Master's module to assess and mark over the holidays !
'PORTUGUESE' DINGHY
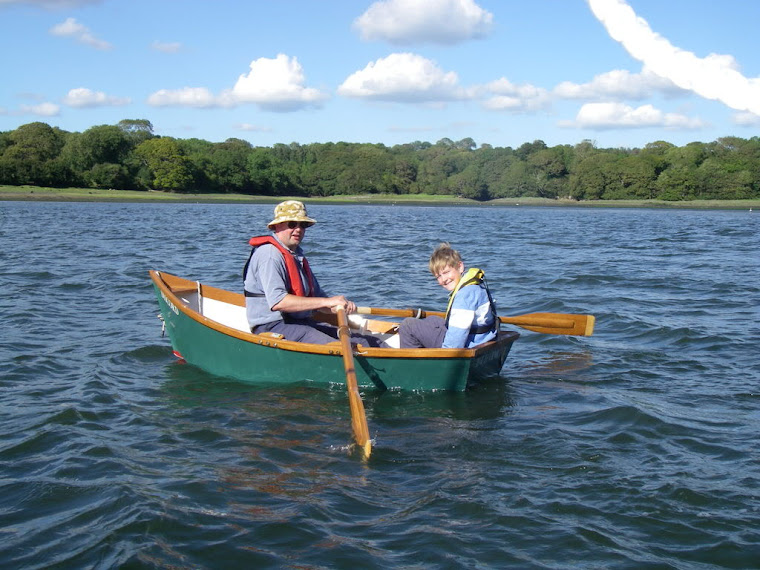
My first build (2007) - designed by Hannu Vartiaala (Hannu's Boatyard)
Friday 20 December 2013
Sunday 15 December 2013
A Weekend's Work
The splice of the deck sheet has worked out well, although - given the low (for UK) temperature - it took over 48 hours for the epoxy to cure:
After which I planed down to the marks all round and then marked out the positions of the bulkheads. Either there is a discrepancy in the plans between the sheet cutting plan and the bulkhead position plan, or I have cut the bow of the deck out 20mm short ! I'm pretty certain its not me as I have checked & re-checked my marking out against the plans before cutting. Whatever, the sheer line is fair and I reckon that I will be able to adjust the side and bottom sheets if necessary.
The next step is to assemble the daggerboard/mast trunk (you can just see it under the bench in the photo above). Here's a better view of it in the process of being dry assembled:
The bulkheads are there to provide reference points and the bow stringer (with 6mm doublers either side of the forward 76mm) forms part of the trunking assembly.
Here's a view of the daggerboard slot:
Getting this the right width (not fully specified in the plans) took quite a bit of calculation - factoring in the thickness of the 2 layers of 12mm ply, glue joint and glassing the sides of the well, plus 3mm play on each side.
Here's as shot of the mast well:
which is easier to calculate (again, not given in the plans) as I know the OD of the mast tube. The packing pieces immediately fore and aft of the well are oak from my offcuts box as I reckon that this area is going to take a fair amount of stress - so I want something tougher than the pine recommended in the plans
To the left of the clamp, there is a complex joint where the bow stringer enters the trunking. This requires some experimentation with packing pieces (no, sizes not in the plans !) to get a good fit:
Once I've got the fit right, I'll tidy up the packers to match the bow stringer, bulkhead and trunking.
Next up will be the glueing up, which I think will be at least a 2 stage process.
After which I planed down to the marks all round and then marked out the positions of the bulkheads. Either there is a discrepancy in the plans between the sheet cutting plan and the bulkhead position plan, or I have cut the bow of the deck out 20mm short ! I'm pretty certain its not me as I have checked & re-checked my marking out against the plans before cutting. Whatever, the sheer line is fair and I reckon that I will be able to adjust the side and bottom sheets if necessary.
The next step is to assemble the daggerboard/mast trunk (you can just see it under the bench in the photo above). Here's a better view of it in the process of being dry assembled:
The bulkheads are there to provide reference points and the bow stringer (with 6mm doublers either side of the forward 76mm) forms part of the trunking assembly.
Here's a view of the daggerboard slot:
Getting this the right width (not fully specified in the plans) took quite a bit of calculation - factoring in the thickness of the 2 layers of 12mm ply, glue joint and glassing the sides of the well, plus 3mm play on each side.
Here's as shot of the mast well:
which is easier to calculate (again, not given in the plans) as I know the OD of the mast tube. The packing pieces immediately fore and aft of the well are oak from my offcuts box as I reckon that this area is going to take a fair amount of stress - so I want something tougher than the pine recommended in the plans
To the left of the clamp, there is a complex joint where the bow stringer enters the trunking. This requires some experimentation with packing pieces (no, sizes not in the plans !) to get a good fit:
Once I've got the fit right, I'll tidy up the packers to match the bow stringer, bulkhead and trunking.
Next up will be the glueing up, which I think will be at least a 2 stage process.
Friday 13 December 2013
Work starts on the deck
The Moonfish is built upside down, using the deck as the reference. I've now spliced together the 2 sheets of 6mm ply that make up the deck:
Before doing this, I dry-fitted and clamped the sheets together so that I could draw the grid and mark out the sheer lines. This, in turn, allowed me to rough-cut to within about an inch of the lines - making the sheets much easier to move around in a confined space.
The sheets are spliced on one side only (upper as you look at it now, but will be the underside of the deck once complete) with 100mm woven tape & epoxy. They are clamped between two boards wrapped (smoothly & tightly) with polythene, which hopefully should give a smooth finish requiring minimum sanding. Poor man's peel ply ! The boards are the 2 sides of the daggerboard/mast trunk - perfect size for the job !
Before doing this, I dry-fitted and clamped the sheets together so that I could draw the grid and mark out the sheer lines. This, in turn, allowed me to rough-cut to within about an inch of the lines - making the sheets much easier to move around in a confined space.
The sheets are spliced on one side only (upper as you look at it now, but will be the underside of the deck once complete) with 100mm woven tape & epoxy. They are clamped between two boards wrapped (smoothly & tightly) with polythene, which hopefully should give a smooth finish requiring minimum sanding. Poor man's peel ply ! The boards are the 2 sides of the daggerboard/mast trunk - perfect size for the job !
Wednesday 11 December 2013
Some thoughts on storage
Space is always at a premium in a small garage. My workshop also has to serve as (in order of volume required):
- A store for the family bicycles
- The garden shed (mower, tools and BBQ)
- Kids' sports equipment store
- Domestic 'root cellar' (bottled water, tins (cans), toilet paper, etc)
- Boot & shoe cleaning facility
All of which require at least some degree of ease of access and protection from dust & other workshop detritus.
This doesn't leave a lot of space (but I have no other) for storage of sheets of ply, lengthy baulks of timber or bulky epoxy. There is no permanent heating (an electric blow heater when I am there), which gives issues with epoxy storage in winter.
The five sheets of ply and 25m of 25x25mm stock pine that I had ordered for the Moonfish build arrived today. The pine was in 4m lengths, which I managed to store under the build bench - but the ply presented a conundrum:
This is 2 sheets of 6mm ply leaning up against the domestic dry goods shelves (protected from dust by polythene sheeting); they can't stay there !
A quick check of the nesting diagram in the plans:
confirmed that it would be OK to slice all but 2 of the sheets in half lengthways. After some careful marking out and setting up a fence, that is what I did with the Skilsaw.
Problem solved; the half sheets now rack up nicely under the build bench:
The remaining 2 full sheets, which will form the deck, are the first to be used in the build process - so will go up on the bench ready to be joined together and marked out.
Things are still tight, but there is room to work - and for all the other users of the space to get at their stuff.
(The epoxy storage issue ? Well, I bodged up a hot box - but that's another post)
- A store for the family bicycles
- The garden shed (mower, tools and BBQ)
- Kids' sports equipment store
- Domestic 'root cellar' (bottled water, tins (cans), toilet paper, etc)
- Boot & shoe cleaning facility
All of which require at least some degree of ease of access and protection from dust & other workshop detritus.
This doesn't leave a lot of space (but I have no other) for storage of sheets of ply, lengthy baulks of timber or bulky epoxy. There is no permanent heating (an electric blow heater when I am there), which gives issues with epoxy storage in winter.
The five sheets of ply and 25m of 25x25mm stock pine that I had ordered for the Moonfish build arrived today. The pine was in 4m lengths, which I managed to store under the build bench - but the ply presented a conundrum:
This is 2 sheets of 6mm ply leaning up against the domestic dry goods shelves (protected from dust by polythene sheeting); they can't stay there !
A quick check of the nesting diagram in the plans:
confirmed that it would be OK to slice all but 2 of the sheets in half lengthways. After some careful marking out and setting up a fence, that is what I did with the Skilsaw.
Problem solved; the half sheets now rack up nicely under the build bench:
The remaining 2 full sheets, which will form the deck, are the first to be used in the build process - so will go up on the bench ready to be joined together and marked out.
Things are still tight, but there is room to work - and for all the other users of the space to get at their stuff.
(The epoxy storage issue ? Well, I bodged up a hot box - but that's another post)
Monday 9 December 2013
Saturday, 30 November 2013
A bit more progress.
This is the main bulkhead which forms the aft part of the dagger board/mast trunk and the forward part of the cockpit:
And theses are the sides of the trunk:
All in 12mm WBP ply. I'm using up some of my workshop offcuts from previous builds and repair work - its surprising how many components fir a small craft like this you can get out of offcuts, which all reduces the cost of the project (not to mention clutter in the workshop !). The frame is going to end up a mix of WBP and Robbins Elite marine ply; the former is more than adequate as the design is explicitly an epoxy/ply sandwich - the latter is overkill in quality terms, but it was lying about in small parts, so .....
I have done more, but not taken the photos yet. There are still quite a few frame components to make before any sort of assembly starts !
A bit more progress: I have now completed all the frame components. I
couldn't resist setting them out roughly, so that I could begin to get a
clearer picture of what I am building.
A view from the stern:
[IMG]
[/IMG]
another from up towards the bow looking at the daggerboard trunk:
[IMG]
[/IMG]
And a final closer view from the stern:
For bulkhead C (the one with the central circular and two rectangular
side cutouts) which is the rear bulkhead of the cockpit well, the design
called for 6mm ply. I had run out of large enough stock scraps for
this, so laminated it from two 4mm layers; I reckon that a little extra
strength at the rear of the cockpit (the forward bulkhead is 12mm) will
be no bad thing.
Somehow this seems bigger than a Laser hull - though they are nominally about the same length.
A view from the stern:
[IMG]
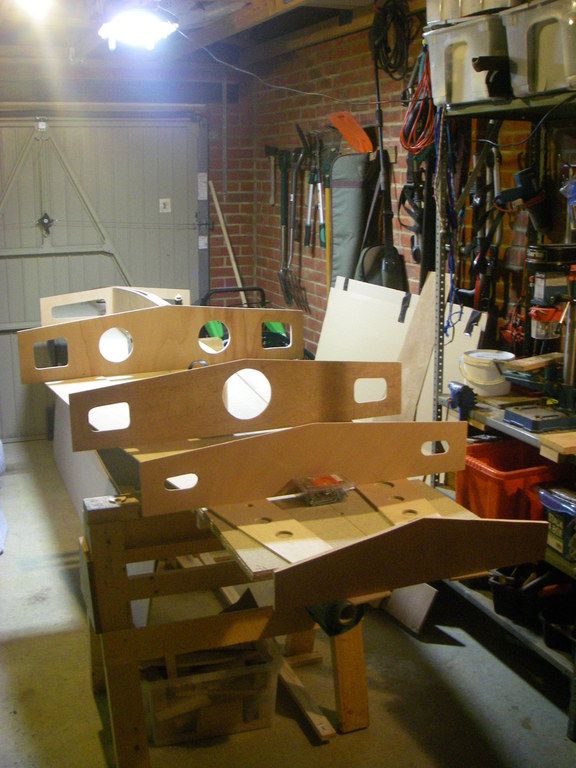
another from up towards the bow looking at the daggerboard trunk:
[IMG]
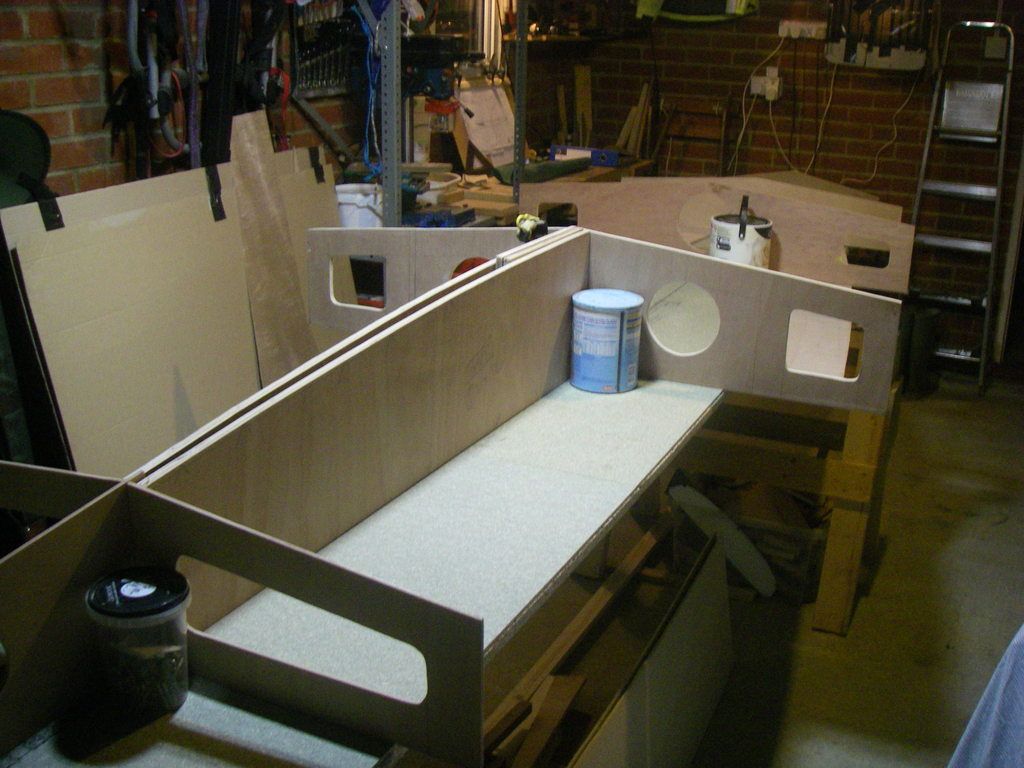
And a final closer view from the stern:
Somehow this seems bigger than a Laser hull - though they are nominally about the same length.
Subscribe to:
Posts (Atom)